IMS International Metal Supply
Automation of Communications through Email and Document Delivery to Improve Efficiency and Customer Service
International Metal Supply (IMS), formerly known as EPUR METAL, is a France-based company specializing in the purchase and sale of non-industrial and recycled metals since 1969.
IMS provides reliable and professional service to international clients, offering high-quality metals for industrial use. Despite being located in France, IMS operates globally, ensuring efficient and personalized management in the trade of metals and raw materials.
The main challenge was to significantly improve the company’s operational efficiency by automating the process of sending essential documents such as invoices, purchase and sales confirmations, and shipping vouchers, as well as optimizing email communications with customers. Previously done manually, these deliveries caused delays, increased the risk of human error, and consumed valuable resources.
The solution involved integrating the new tools from the automated document generation system with the email platform and existing databases. This enabled relevant information to be extracted directly from the databases and sent automatically and at the right time, ensuring documents reach clients precisely when needed.
The goal was to eliminate repetitive tasks, reduce response times, and ensure accurate and smooth communication with clients, thereby enhancing satisfaction and efficiency throughout the process.
With the automation of communications and of document management, we can achieve more precise and efficient communication, reducing response times and errors
Our Solution
The company handles daily communications and sends key documents to clients, which must be delivered correctly and on time. Additionally, accounting documents must be accurate and sent promptly to avoid errors that could lead to payment issues, lost sales, or even the loss of important clients. In this analysis, we identified critical points in the current processes to establish automation goals that would enhance efficiency and streamline communications.
Following the analysis, specific tools were selected to be integrated with the company’s internal systems. Make was used for workflow automation, and Parseur was used to extract data from documents and emails. These tools were chosen to ensure efficient and accurate management with lower resource costs.
Once the new tools were set up, new communication flows were created. Various tools and databases were connected through Make, establishing a new digital environment for the company and reducing employees’ repetitive tasks.
Documents are sent to clients automatically, with delivery triggered as soon as transaction or shipment data is completed or updated.
Employees receive notifications about documents and transaction data, including any client information errors. Errors are identified faster to avoid issues.
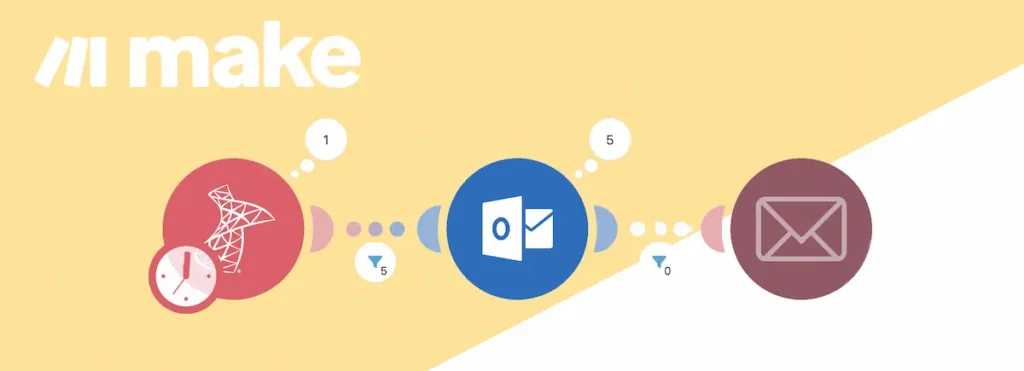
During setup, tests were conducted to ensure the automation worked flawlessly. Tests were run on document and email delivery, verifying that data was extracted correctly and each document reached its destination on time and without errors.
Documentation was created at this stage to explain the functionality of these flows, enabling future modifications.
Automatic checks were also set up to verify that documents are sent consistently, identifying errors and issues more quickly.